aluminum foil
Aluminium foil is a solid sheet of aluminium of a suitable alloy, rolled to very thin thicknesses, with a minimum thickness of about 4.3 microns and a maximum thickness of about 150 microns. From a packaging and other major application point of view,
One of the most important properties of aluminum foil is its impermeability to water vapor and gases. Dies 25 microns or thicker are fully waterproof. Thinner gauges are laminated to an impermeable composite film ideal for packaging and general insulation and/or barrier applications.
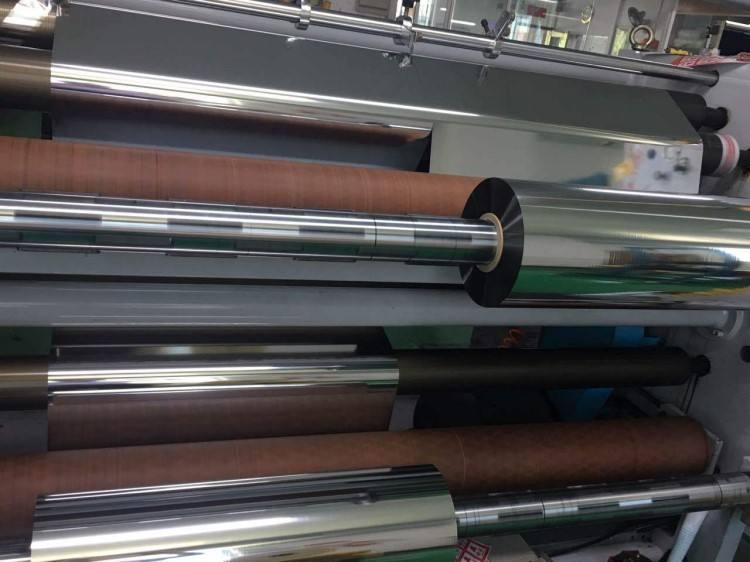
Aluminum foil is available in glossy and matt surfaces. A shiny finish is created when the aluminium is rolled in the final stage. It is difficult to produce rolls with a thin enough gap to make aluminum foil, so in final lamination, both sheets are rolled up at the same time, doubling the thickness at the entrance of the roll. Later when the leaves are separated, the inner surface is matte and the outer surface is glossy.
Aluminum is highly resistant to most greases, petroleum oils and organic solvents.
There are three different groups of alloys on the market, each with different properties. Therefore, it is important to choose the most suitable alloy for each end application.
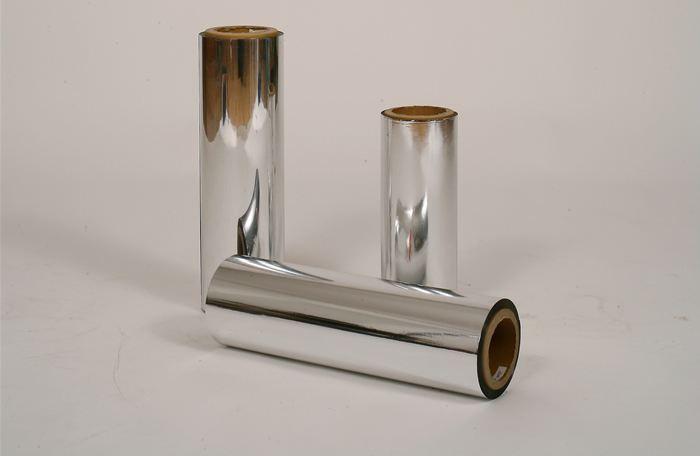
alloy:
– 1235: In this alloy, the aluminum content is very high. The ductility of pure aluminium allows very good transformation behaviour during lamination, making it ideal for producing very thin foils, 6-9 microns.
The minimum amount of alloying elements results in a very low content of intermetallic phases, thus reducing the number of microperforations.
Material hardness is not critical for this particular end use, as thin foils are never used without support. That is, not part of a multilayer compound. Aluminium sheets act as a barrier in the structure, while layers of paper or plastic provide
mechanical resistance.
Typical end uses for this combination of gold are aseptic liquid packaging,
Cigarette paper or coffee packaging.
– 8079: It is an alloy of aluminum and iron (Fe). Iron as an alloying element increases the strength of the foil, which also requires higher transformation forces during rolling. The larger the number and size of Al-Fe intermetallic compounds, the greater the
The greater the risk of microperforation.
As a result, alloyed iron products are most commonly used in products with thicknesses greater than 12 microns and are ideal for non-rolled applications. On the other hand, with the help of intermetallic compounds, a very fine metal grain structure is formed, which makes the product highly ductile and thus achieves high elongation and burst strength values.
This property is necessary for applications where the structure is folded multiple times and the aluminum sheet must have sufficient elongation to deform in the bending area without breaking.
The most representative end uses are cold-formed blister packs, bottle caps and chocolate wrappers.
– 8011: It is an aluminum-iron-manganese alloy. The addition of manganese increases the strength of the aluminum foil. Ferromanganese alloys are suitable where very high strength is required.
Al-Fe-Mn alloys are typically used for products where elongation reduction is not critical, but strength is critical for the compound or necessary for the transformation process.
Aluminum foil is widely used in food and pharmaceutical packaging because it completely blocks light and oxygen (causing fat oxidation or rancidity), odor and taste, moisture and bacteria. Aluminium foil is used to make long-life packaging (aseptic packaging) for beverages and dairy products that can be stored without refrigeration.
Foil laminates are also used to package many other oxygen- or moisture-sensitive foods, tobacco, in the form of bags, envelopes, and tubes, as well as tamper-resistant closures.
Foil containers and trays are used for baking baked goods and packaging takeaways, ready-to-eat treats and pet food.
Aluminum foil is also widely used for thermal insulation (barrier and reflective), heat exchangers (thermal conduction) and cable jacketing (for its barrier and electrical conductivity).
– General flexible container
– Pasteurizable containers (retort)
– for Tetra-type containers
– with heat seal coating
– with self-adhesive coating
– household
– Capacitors
– Video cable
- Gold or other colors
– Coated for pharmaceutical blister
– Embossing
– with PE coating
– for chocolate coins
– Corrugated
– with non-stick coating
– Coated for cheese packaging
– Beer bottle caps –
toothpaste tube
– for heat exchangers
Aluminum foil comes in different formats:
Available alloys:
– 1235
– 8011
– 8079
– Thickness: Typical commercial thicknesses are 6 microns to 80 microns. Other indicators should be referenced.
– Different temples, the most commonly used are H-0 (soft) and H-18 (hard).
– Application: Sheets for certain applications, such as retortable containers, pharmaceutical containers, etc., require special microporous specifications.
– Wettability: Class A
– Use a different type of coating if necessary. Can be heat sealed, colored, printed, embossed, corrugated, etc.
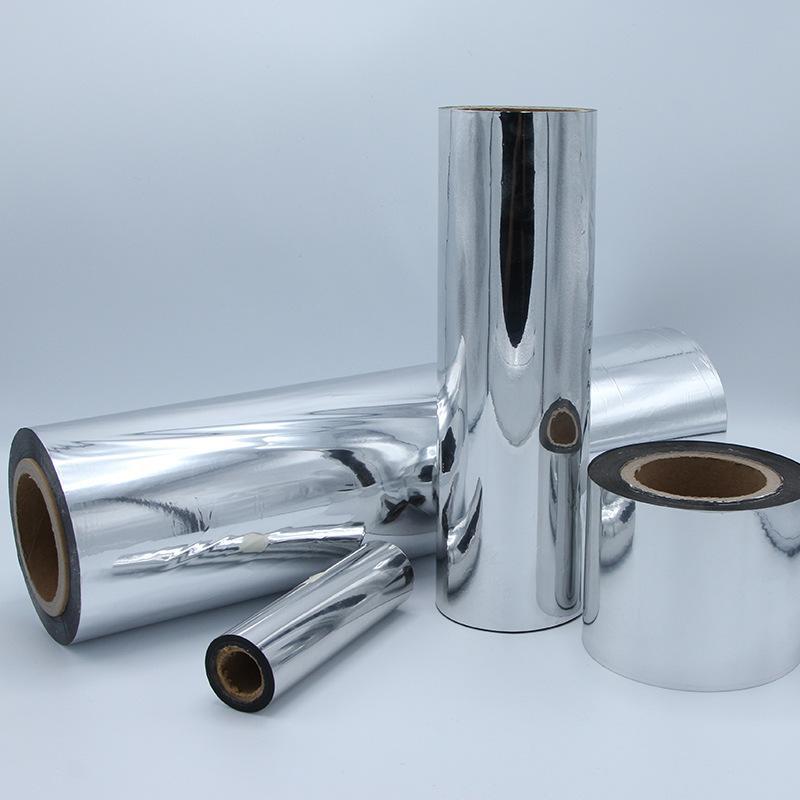
Post time: Jan-06-2024